Sergio Flores Velez
Central Washington University Student
Mechanical Engineering Technology
Senior Project
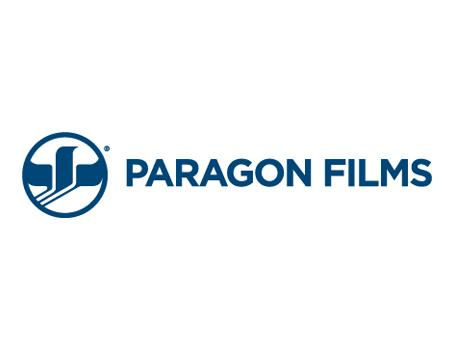
Senior Project Abstract
Paragon Films has always strived to increase productivity and decrease waist within their company. The plant located in Union Gap, Washington currently has two production lines operating 24/7. Each line is handled and supervised by two, maybe three, people during each shift. The bigger production line produces the machine films, which are generally heavier and larger ranging from 5000 to 10000 revolutions per roll. This production line, the bigger one, has a three part system that automatically feeds the paper cores to the spool shafts to roll the films. One part of the system, a core bin, can hold about 400 cores at a time. So, the employees during that shift don’t have to worry about filling up the bin very often. On the other hand, the second production line, which produces the hand films, does not have a system that can feed paper cores to the spool shaft. This smaller production line has a table attached to it which holds only 60 cores at a time. This means that the employee has to constantly go around to the attached table and manually set cores on the table. The drive of this project was to design and manufacture a similar Core Feeder that would automatically feed the cores to the table. This design had size restriction due to the limited space by the production line but would still manage to improve productivity in the plant. The design also took into account the amount of time it will be active so precautions were taken to select durable material to avoid early failures within the system.
![]() | ![]() |
---|---|
![]() | ![]() |
![]() | ![]() |
![]() | ![]() |
![]() | ![]() |
![]() | ![]() |
![]() | ![]() |
![]() | ![]() |
![]() | ![]() |
![]() | ![]() |
![]() | ![]() |
![]() |